There are many decoration techniques for branded and custom mugs, we take a look at the dye sublimation process and see how it works.
There are many methods of branding promotional products like mugs, but one of the most popular techniques is dye sublimation. But what is dye sublimation? Within the promotional gifts industry, it is often assumed that those ordering branded mugs or other promotional products understand the different techniques used for customising your promotional products and the benefits and disadvantages that different methods bring.
However, this is not always the case. We take a look at the dye sublimation process and explain the technical details of this decorating technique for promotional mugs to illuminate the decorating process.
What is Dye Sublimation?
Dye sublimation is a digital method of applying an image to specially coated ceramics, metals and polyester fabrics to name but a few of the substrates used. It allows for photo quality images to be printed on to many promotional products. This quick and effective digital print method is replacing screen printing practices for shorter production runs and for output that requires multiple colours and photographic images. It also has a wider colour gamut available compared to screen printing with ceramic inks and allows for printing halftones and tints.
The Dye Sublimation Production Process:
There are many printers available for the dye sublimation process, and they are not too different from desktop colour inkjet printers. The main difference is the inks used. Dye sublimation uses specialised inks, which has the unique ability to convert from a solid to a gas without going through a liquid form.
The first step of the process is to print your design on to transfer paper. Dye sublimation transfer paper is a speciality paper. It absorbs and holds the ink, the ink is dry to the touch but slight moisture can damage the print, such as moisture from finger tips. Once you have printed your transfer paper, the paper is then placed on to the promotional mug.
For the image to transfer from the paper on to the mug, there must be both pressure and heat. At Prince William Pottery, we position the transfer using heat resistant tape and this also creates the pressure. The mugs with the transfer paper are then put on a conveyor convection oven. The oven is heated to approx. 200C and the heating process takes approximately 20 minutes. The heat turns the ink into a gas and at the same time the special coating on the ceramic mugs allows the gas to enter. This is why pressure is important, as when the ink turns to gas the pressure directs the gases to where the ink needs to go.
When the temperature drops, the gas returns to being a solid and the print becomes part of the coating. The transfer is then removed from the mug and the decorating process is completed.
One issue facing dye sublimation is the inability to print white ink. This means that the process only works on white or light coloured promotional products. Within the scope of promotional mugs, there is the ability to print dye sublimation onto black mugs. To achieve this a white panel has to be screen-printed on to the mug first before it is coated. The design is then limited to the size of the white panel.
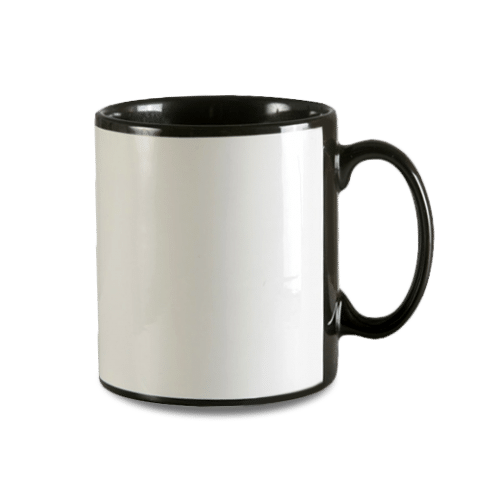
Dye Sublimation At Prince William Pottery:
At Prince William Pottery we have two dye sublimation printers allowing us to print up to 4,000 transfers a day, this allows us to produce your branded mugs quickly even with the tightest of deadlines.
If you want to learn more about our dye sublimation mugs please contact us on 0151 259 1221 or e-mail
0 Comments